THE FIELD ENGINEERING TEAM PROPOSES ALTERNATIVE MANUFACTURING PROCESS TO ADDRESS COST ISSUES WITH THE CURRENT DESIGN.
Challenge
A customer of Field’s was looking to reduce the cost of their three highest cost components. The tolerances on the customer’s print could only be met by fully machining the components. The machining process is slower than cold forming and creates more raw material scrap.
Solution
The Field engineering team proposed revising the tolerances to utilize the cold forming process instead of the machining process. Field’s engineers collaborated with the customer’s design team to ensure the new tolerances would still meet all design and joint requirements. The Field team also set the expectation with the customer as to what they could expect from a cold headed component versus a fully machined component. The new tolerances and appearance were approved by the customer and samples were ordered.
Results
The samples met the customer’s performance and design requirements and full production was approved.
- Stronger Components
- Improved Pricing
- Reduced Raw Material Scrap
REDESIGN PIECE PRICE SAVINGS: 48%
ANNUAL SAVINGS: $416,102
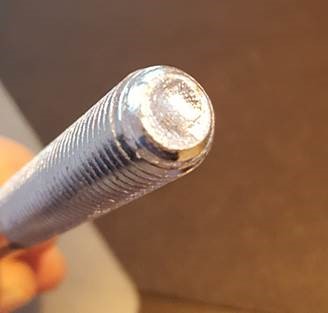
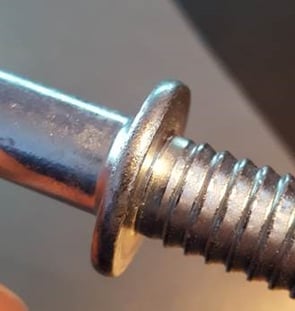